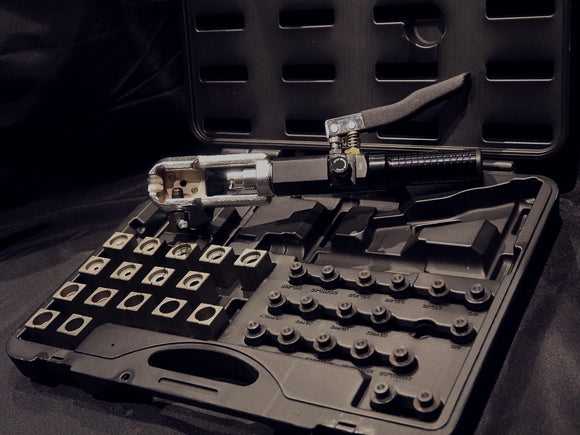
Fittings with Flare: A Guide to the Universal Hydraulic Flaring Tool
4Lifetimelines can't say that there is a catch-all way to fix every automotive problem with a single tool, but we know that it's important to provide useful tools that can be used for a variety of situations. A shop is full of hundreds of pieces, parts, tools, and equipment, and nearly any way to cut down on the number of things floating around is a way worth taking. That's why we provide the Universal Hydraulic Flaring Tool. It's a useful piece of equipment that cuts down on flaring time and can be used to fabricate flares for fuel, A/C, and brake lines all in one toolkit. There's only one problem with tools that are as complex as the UHFT, though: the complicated operation of the tool itself. There is a litany of operations that the tool can facilitate, and so 4LTL is publishing this guide to help explain the tool further.

The Universal Hydraulic flaring tool is a multi-faceted tool capable of flaring basically any line necessary for brake and fuel line replacement. Its uses are varied, but it is indispensable to a shop that frequently repairs or replaces lines of any type. The tool comes with many dies and is designed to handle flares for 45-degree inverted, Bubble ISO, Push-connect, GM Fuel, and GM Transmission flaring. Single flares can also be fabricated for lower-pressure lines.
The tool itself comes split into 4 parts: The Yoke, the Yoke Handle, the Hydraulic Handle, and the Clamping Screw Rod. The plunger is threaded so that the yoke can screw onto the handle. Assembling the tool is fairly straightforward: slide the clamping screw rod into the clamping screw, screw the yoke onto the hydraulic handle, and then thread the yoke handle into the hole on the bottom of the yoke. From there, the tool is assembled and may be used for flaring.

The Universal Hydraulic Flaring Tool is operated by closing the hydraulic system inside the handle and pumping. This projects the plunger forward into the yoke, which holds the die set. When flaring, the tubing is fit into the die set that matches the tubing's outer diameter, and together these two parts are placed into the yoke. The die set is then secured into the yoke by twisting the clamping screw. A die inserted into the end of the plunger then forms the tubing held within the die set into the desired shape of flare.

Once the tubing is secured into the yoke the flaring process begins. First, the release knob (labeled close and open) is turned to "close", and then the OP 0 die is loaded into the plunger.

The tubing is then slotted into the die set and placed into the yoke. It is important that the tubing be flush or at least slightly past the edge of the die set when it is placed into the yoke.


After the die set is placed into the yoke, the Clamping Screw may be tightened. Do not tighten down too much, as the OP 0 die is used to align the tubing flush with the face of the female die and the tubing needs to be able to move within the die set for this to happen.

To align the tube flush with the die pump the handle once the die is set and the plunger die is set until it becomes very difficult to squeeze. Once this happens, the tube is aligned flush, and the release knob can be turned to open. This will retract the plunger. This is a universal process for every flare and can be used at the start of each flaring operation.
From here, the process diverges. Depending on the flare shape desired, the die will be different: a double flare will use the flare labeled simply with the imperial measurements of the tubing's outer diameter, while other dies will be labeled with other details that connote their corresponding flare (i.e. ISO, CONNECT, and GM FUEL). Regardless of the flare, the second stage will be labeled "OP1". The dimensions and purpose of each die are labeled in the box and embossed into the side of the die. Once the new die is loaded, the hydraulic handle can be closed and pumped until the lever once again becomes difficult to actuate. From there, the knob can be turned to open. This will retract the plunger.

Depending on the flare, there will also be an OP 2 die that must be slotted into the plunger, and the whole process is repeated. This is the case for double flares. Once the last step of the flare-forming process is completed, the plunger can be retracted, the clamping screw released, and the die set can be extracted from the yoke. At this point, the line should be flared!

There are a few problems that can happen when flaring a line. The flare might form off-center from the line, the die set might slip, or more problematic: the line could get stuck in the die. Each of these potential problems has an answer. If a flare forms off-center, it is likely that the tubing was not straight or unevenly work-hardened. If the tubing slips in the die set, it is likely that the clamping screw was not torqued enough or that the surface of the tubing has been worn smooth somehow. The worst problem is when the tubing gets stuck inside of the die: this is likely because the tubing itself was not sized to specs and had an abnormally-large outer diameter. If this happens, work the line around in the die until it comes free. With longer flares like GM lines, this may be more difficult but can be done with a pair of pliers, a vice, and a nice mallet.

The 4LTL team loves the Universal Hydraulic Flaring Tool. It's quick to use, produces great flares, and has a lot of utility in the shop. It can even be used with just one hand if you're clever.
We hope this guide has been helpful and informative!
Did you enjoy reading our blog? If so, let us know by using promo code: BLOG10 at checkout and get 10% off of your order!
Best of luck with your next project,
the 4LTL Team