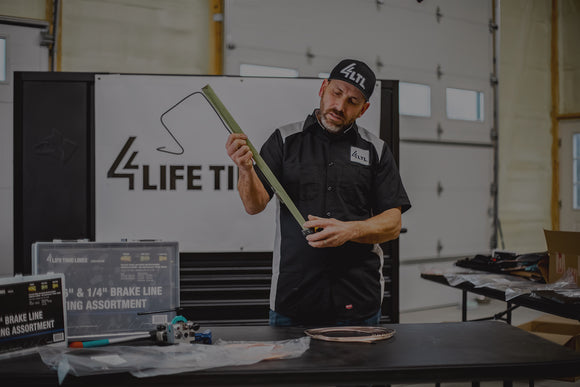
All about Hydraulic Brake Systems
When we hit the brakes, we really don’t think much about the chain of mechanisms that activate to stop the vehicle. What really happens in the hydraulic braking system? The short answer is that the brake pedal moves hydraulic fluid like a flexible stilt between the driver and the brake calipers. The long answer is more complicated, so buckle up-- things are about to get dense.
When the brake pedal is depressed it actuates an arm connected to a part called the Master Cylinder. This master cylinder controls hydraulic pressure across the whole brake system. Between the brake pedal and the hydraulic cylinder it operates, mechanical energy is converted to hydraulic energy.
The way hydraulic systems are, they're considered closed-loop: no fluid leaves, no fluid enters. Unless there's a leak, of course. Otherwise, though, hydraulic fluid doesn't compress, but rather transmits energy by moving brake fluid under pressure. This is how the brakes work like a flexible stilt, as we referenced earlier; rather than a wooden or metal rod being used to apply pressure to the brakes, fluid is moved across a set of tubing lines mounted across the car. These tubing lines are referred to as brake lines, and act as conduits for the hydraulic fluid.
Once the brake pedal is depressed, the brake fluid moves through the brake lines and enters the calipers and wheel cylinders, flowing to the pistons inside and actuating the pistons. As the brake caliper or wheel cylinder pistons move, they push the brake friction pads and shoes. The pads and shoes then make contact with the brake rotors or brake drums, which are rotating at the speed of the wheels and tires at the time of braking. This contact creates friction that works to slow the vehicle.
Hydraulic brakes were first patented around 1917, and have been the standard for braking systems since then. In the simplest form, a single hydraulic circuit from the master cylinder out to the wheels provided pressure that was regulated only by the operator’s foot pressure. These early systems incorporated none of the safety considerations found in modern passenger automobiles, and could be quite unsafe given that any component or brake line failure would result in a total loss of all braking.
These days, automated systems within most vehicles govern braking activities in emergencies. Diagonal split systems (AKA dual diagonal) became mandatory in 1976 and required that the master cylinder split the hydraulics so that even with a hydraulic failure the vehicle could still stop. In a dual-diagonal system the front right and rear left are typically controlled by one hydraulic circuit and the front left and rear right by the other. With dual-diagonal systems, a failure in one circuit will still allow the vehicle to stop, albeit under reduced braking power.
Hydraulic brakes give today’s passenger vehicles tremendous stopping power, but it’s critical to maintain the system with regular brake fluid exchanges to retain high boiling point and prevent internal rust, sediment and corrosion. Exchanging the brake fluid every two years is a good rule of thumb to prevent issues. Mineral-based brake fluid absorbs atmospheric moisture over time and as the brake fluid becomes more saturated with moisture, the boiling point will be greatly reduced. Because brake friction causes heat, brake fluid with high moisture content can boil inside the brake calipers and wheel cylinders, resulting in air pockets that can compromise braking effectiveness.
In addition to the dangers posed by fluid boiling, moisture in the brake fluid can rust and make steel brake lines pitted and prone to leak or fail. This can also happen internally to calipers and wheel cylinders. One of the greatest requirements of any hydraulic brake system is clean, dry brake fluid!
Our final thought on brake system hydraulic requirements is on brake line and brake hose integrity. Brake lines and hoses must endure countless thousands of hydraulic pressure cycles, environmental exposure, and the general stresses and strains of flexing during operation. Brake hoses connect the hard brake lines to the brake calipers and to the differential in rear-wheel drive vehicles. They must flex as the suspension moves and are subject to wear from stress at connection points, atmospheric UV light, and ozone. Internal decomposition over time is also a significant factor in brake hose composition.
Brake lines connect various brake system components and are configured with flared tube ends and tube nuts that attach the hard lines to components. Each part of the brake line must be able to withstand thousands of pounds of pressurized force. Original equipment hard lines are typically made using plated or coated mild steel tubing. Unfortunately, this tubing rust from exposure to road salts, moisture, and debris that accumulates on or around them over time. Original equipment steel tubing that is weakened by rust can fail catastrophically and unexpectedly, so make sure to check your brake lines often! You can find more about how to do that with our post on brake line maintenance. Here at 4LTL, we offer a variety of tubing which is specifically designed to outlast all of the conditions brake lines have to endure: Copper-nickel brake line tubing. It's malleable and ductile, yet strong and rust-proof. 4LTL endorses it as the best option for brake line installation. You can read more about it here!
4LTL is proud to be a part of the automotive aftermarket, and we hope that this information has helped you understand the intricacies of your vehicle's brake line system.
Did you enjoy reading our blog? If so, let us know by using promo code: BLOG10 at checkout and get 10% off of your order!
Best of luck on your next project,
The 4LTL team